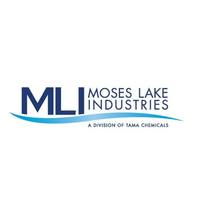
Description
We value: Safety, Integrity, Ownership, Collaboration, Service, Sustainability
Moses Lake Industries, Inc. (MLI) is a rapidly growing producer of ultra-pure chemical products, serving the semiconductor and flat-panel screen industries worldwide. We deliver world class products to the leaders of the industries we serve.
You will be working for a midsized company with great people and a history of steady growth and profitability. Sound like a match? If you are prepared to work in an exciting and rewarding environment, we look forward to considering your experience and qualifications.
Shift/Hours/Location: 8AM–5PM, onsite Mesa, AZ
WHAT YOU WILL BE WORKING ON
- Safe lab environment free of any mitigatable safety risks while driving compliance to MLI and Lab safety programs through you and your leadership team role modeling behavior and leading safety. Includes compliance to a robust PPE & Hygiene process & application current with MLI EHSS requirements.
- Ensure sufficient staff to operate lab at optimum production to meet volume requirements across all shifts while maintaining strict headcount targets.
- Development roadmaps for staff for professional development, growth, or area for improvement.
- Certified & trained resource back-up and redundancy across all roles, titles, shifts & hours. Compliance of lab staff to Training metrics including L1, L2, L3 training & certification dates for applicable equipment/processes in partnership with Lab Technical Trainer. Compliance to training roadmaps
- Explore, Plan, Develop, Deploy, Continuously Improve relevant metrics including samples p/labor hour, samples p/person, samples p/tool, samples p/lab, Transactional Defects Per Million (based on retainer requests and resampling separately), Perfect Order Index (POI) and other key measures as identified.
- Activate and manage lab monitors/tv's with relevant information: PM schedule, KPI's, Production Schedule, Utilization/Capacity/Tool Uptime & Tool Downtime
- Continual benchmark of lab production and operations against market and industry data, maintaining a roadmap of gaps and actions. Drive continuous improvement projects (CIP) to recommend/propose solutions to adopt across all MLI labs.
- Third level of single-point-of-contact for production and escalations
- Point-of-contact for NCR/CAPA's and facilitation of problem solving to make & meeting due date commitments with thorough application of root cause problem solving. Participates and creates presentations for problem solving investigations. Works with Technical Team Lead, Supervisor, & Manager to direct certified staff with action items.
- Point-of-contact for FMEA/PFMEA, CIP, OpEx and other related committee's or projects tied to the lab.
- Develop performance reviews (90 day, semi-annual, annual) of Team Leads & Technical Leads for Manager review and approval. Review and approval of lab team member level reviews, verbal, written, PIP/PEP, Last/Final warning with review and delivery with Manager.
- Maintain laboratory environment in a clean and organized manner following strict laboratory chemical hygiene standards (following Lean 5S methodology) including emptying of trash, sweeping & mopping floors, and cleaning of glassware.
- Follows established safety protocols.
- Maintains a willingness to follow guidance and training from certified staff.
- Communicate effectively with other team members to ensure effective laboratory operations.
- Other duties as assigned to promote a high functioning team.
- Uphold all MLI policies and “MLI Code of Conduct.” With the understanding that everyone will be treated with the utmost courtesy and respect regardless of position or stature. Every employee has an affirmative duty to immediately raise harassment concerns to Company management.
- Strict compliance with Environmental and Safety regulations. Strong commitment to safety and ongoing demonstration of good chemical hygiene practices.
- Compliance and individual accountability with the MLI Quality System and ISO Registration is required. It is the employee's commitment to ensure that the Company's actual practices and procedures are exercised as directed.
QUALIFICATIONS
- High School diploma or General Educational Development (GED).
- Associate degree, prefer bachelor's degree or equivalent.
- If degreed, > 5 years lab experience. If no degree > 10 years lab experience with leadership/management responsibility
- Ability to read, understand apply information in Safety Data Sheets to ensure safe handling and use of chemicals and laboratory apparatus.
- Computer literacy including ability to use software with working knowledge of computers and MS Office software.
- Regular and punctual attendance is expected to accomplish the critical mission of the department and organization.
- Perform necessary tasks and work hours needed to accomplish department and company goals.
- Work as a productive member of a cohesive group toward a common goal and contribute to team development and effective team dynamics.
- Ability to plan, organize and carry out assignments as instructed and with attention to detail and accuracy and in a timely manner.
- Effective written and verbal communications skills, in English.
- Ability to stand and walk for long periods of time.
- Demonstrated ability to:
- Always maintain a high level of integrity while being courteous, tactful, and cooperative with co-workers, management, and customers both internal and external.
- Respond positively and effectively to rapidly changing priorities and departmental needs.
- Manage multiple priorities and projects simultaneously to meet established deadlines.
SALARY & BENEFITS
Please note that the salary information shown below is a general guideline only. Salaries are based upon candidate experience and qualifications, as well as market and business considerations.
Summary pay range: $72K-$95K
Located in Mesa, AZ, we offer the following benefits: compensation, medical, vision, and dental insurance benefits.
- Generous PTO: Your off time is important.
- Medical/Dental/Vision: Majority of premiums paid by MLI. Includes virtual medical and mental health options.
- Additional Health Coverage: FSA and HSA available. Voluntary insurance options include life and AD&D, accident, hospitalization, and critical illness.
- Earn More: We offer a generous discretionary bonus program in addition to salary/wage.
- 401(k) Savings Plan: Jump start your retirement with MLI's employer matching contributions.
- Company-Paid Benefits: Long-Term Disability Insurance, EAP, Fitness Club Membership Program, & Education Assistance Program. Relocation Assistance available.
- Additional Benefits: We provide position-based clothing, travel expenses, training and additional materials needed on a case-by-case basis.
WORKING CONDITIONS
Duties are generally performed indoors, in a 24-hour per day, seven days per week manufacturing and laboratory environment. Handling and working with hazardous materials and chemical manufacturing equipment is routine. The employee may work in the presence of fumes or airborne particles, hot, toxic or corrosive chemicals, water, liquids and electrical equipment. Employees will work in a covered Process Safety Management (PSM) environment containing threshold quantities of flammable liquids and/or gasses that have a potential for fire or explosion. Employees working in this environment are required to be free from devices that are not considered intrinsically safe. Examples of devices that may not be intrinsically safe include Insulin Pumps, Pacemakers, Pain Management devices, etc. The noise level in the work environment is occasionally loud. When working in the presence of these hazards, the employee is expected to follow company safety rules and use proper personal protection such as: hardhat, respirator, hearing protection, protective clothing, safety glasses, safety footwear, etc.
Qualifications
Required Knowledge, Skills, and Ability:
- High School diploma or General Educational Development (GED).
- Associate degree, prefer bachelor's degree or equivalent
- If degreed, > 5 years lab experience. If no degree > 10 years lab experience with leadership/management responsibility
- Ability to read, understand apply information in Safety Data Sheets to ensure safe handling and use of chemicals and laboratory apparatus.
- Computer literacy including ability to use software with working knowledge of computers and MS Office software.
- Regular and punctual attendance is expected to accomplish the critical mission of the department and organization.
- Perform necessary tasks and work hours needed to accomplish department and company goals.
- Work as a productive member of a cohesive group toward a common goal and contribute to team development and effective team dynamics.
- Ability to plan, organize and carry out assignments as instructed and with attention to detail and accuracy and in a timely manner.
- Effective written and verbal communications skills, in English.
- Ability to stand and walk for long periods of time.
- Demonstrated ability to:
- Always maintain a high level of integrity while being courteous, tactful, and cooperative with co-workers, management, and customers both internal and external.
- Respond positively and effectively to rapidly changing priorities and departmental needs.
- Manage multiple priorities and projects simultaneously to meet established deadlines.
- Continual benchmark of lab production and operations against market and industry data, maintaining a roadmap of gaps and actions. Drive continuous improvement projects (CIP) to recommend/propose solutions to adopt across all MLI labs.
- Third level of single-point-of-contact for production and escalations
- Point-of-contact for NCR/CAPA's and facilitation of problem solving to make & meeting due date commitments with thorough application of root cause problem solving. Participates and creates presentations for problem solving investigations. Works with Technical Team Lead, Supervisor, & Manager to direct certified staff with action items.
- Point-of-contact for FMEA/PFMEA, CIP, OpEx and other related committee's or projects tied to the lab.
- Develop performance reviews (90 day, semi-annual, annual) of Team Leads & Technical Leads for Manager review and approval. Review and approval of lab team member level reviews, verbal, written, PIP/PEP, Last/Final warning with review and delivery with Manager.
- Maintain laboratory environment in a clean and organized manner following strict laboratory chemical hygiene standards (following Lean 5S methodology) including emptying of trash, sweeping & mopping floors, and cleaning of glassware.
- Follows established safety protocols.
- Maintains a willingness to follow guidance and training from certified staff.
- Communicate effectively with other team members to ensure effective laboratory operations.
- Other duties as assigned to promote a high functioning team.
Apply on company website